Ball, Rod, and Pebble Mills
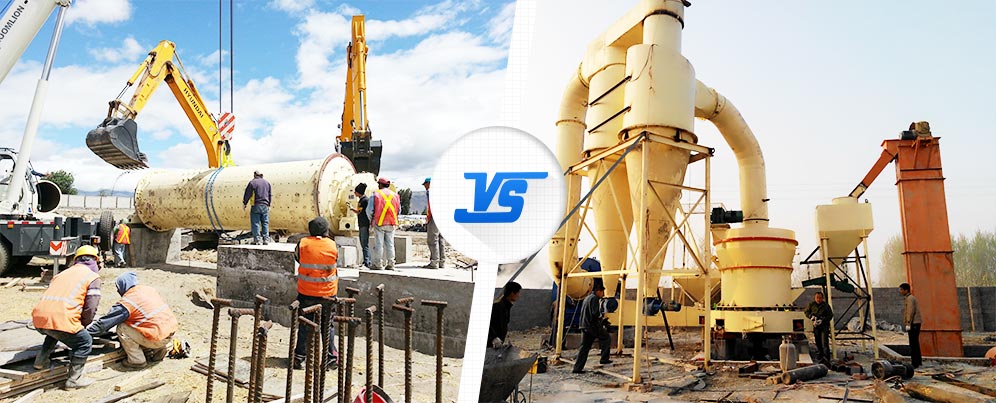
Ball mills are the most commonly used mills for grinding materials in a mill circuit. They differ in design and operating characteristics, but all consists of a cylindrical chamber filled with grinding media, such as steel balls or rods. Rod mills are similar to ball mills in design and structure, but use rods as the grinding media. Pebble mills are similar to ball mills, but use small pebbles instead of steel balls as the grinding media.
Ball Loads
The ball load in a ball mill is the weight of the grinding media, along with the material to be ground. A typical ball mill has a ball load of about 40%, which is a mixture of steel balls and other materials. The ball load affects the grinding efficiency and the power consumption of a ball mill.
Screens and Flakiness
Screens are used in ball mills to control the size of the particles being ground. Flakiness refers to the percentage of particles that are elongated. A high percentage of flakiness indicates poor grinding performance, while a low percentage of flakiness indicates good grinding performance.
Units of Surface
The units of surface describe the total surface area of the particles being ground. A mill can be efficient in grinding small particles with a large surface area, compared to grinding large particles with a small surface area.
Batch and Continuous Grinding Compared
Batch grinding refers to the grinding of a fixed amount of material in a ball mill for a fixed time. Continuous grinding refers to the grinding of an unlimited amount of material in a ball mill. Continuous grinding is more efficient and produces a finer product than batch grinding.
Batch Ball Milling at Various Speeds and Ore Charges
The speed and charge of a batch ball mill affects the grinding efficiency and the product size. Increasing the speed increases the impact energy of the grinding media, while increasing the charge increases the quantity of grinding media.
Best Wet and Dry Batch Ball Milling
Wet ball milling is more efficient than dry ball milling when grinding a relatively soft material, but dry ball milling is more efficient when grinding a hard material.
Selection of Volume of Ball Loads in Continuous Dry Open Circuit Grinding
The volume of ball loads in a continuous dry open circuit grinding operation affects the grinding efficiency and the product size. A higher volume of ball loads produces a finer product with higher grinding efficiency.
Nonferrous Media and Steel Balls Compared
Nonferrous grinding media, such as ceramic balls, increase the grinding efficiency and reduce the wear of the mill liners compared to steel balls.
Sillimanite Balls
Sillimanite balls are a type of nonferrous grinding media that have been used in the grinding of minerals. These balls are harder than steel and have a higher density, which results in a more efficient grinding process.
Tetrahedrons and Spherical Balls Compared
Tetrahedrons are a type of nonferrous grinding media that have been used in the grinding of minerals. These balls have a higher density and a more uniform shape compared to spherical balls, resulting in a more efficient grinding process.
Battered Reject Balls and New Balls Compared
Battered reject balls are steel balls that have worn out and cannot be used for grinding anymore. New balls are unused steel balls used for grinding. Battered reject balls reduce the grinding efficiency compared to new balls, resulting in a coarser product and higher wear of the mill liners.
In conclusion, a ball grinding mill is a vital piece of equipment used in various industries for grinding and blending materials. The efficiency of a ball mill is affected by various factors such as the ball load, grinding media type, and the speed and charge of the mill. By understanding these factors, you can optimize the performance of a ball mill and produce a finer product with higher grinding efficiency.